Customer Spotlight: AkzoNobel
A B2B/B2C inriver case study
Read how inriver and implementation partners CTAC gave AkzoNobel’s product data management a fresh lick of paint.
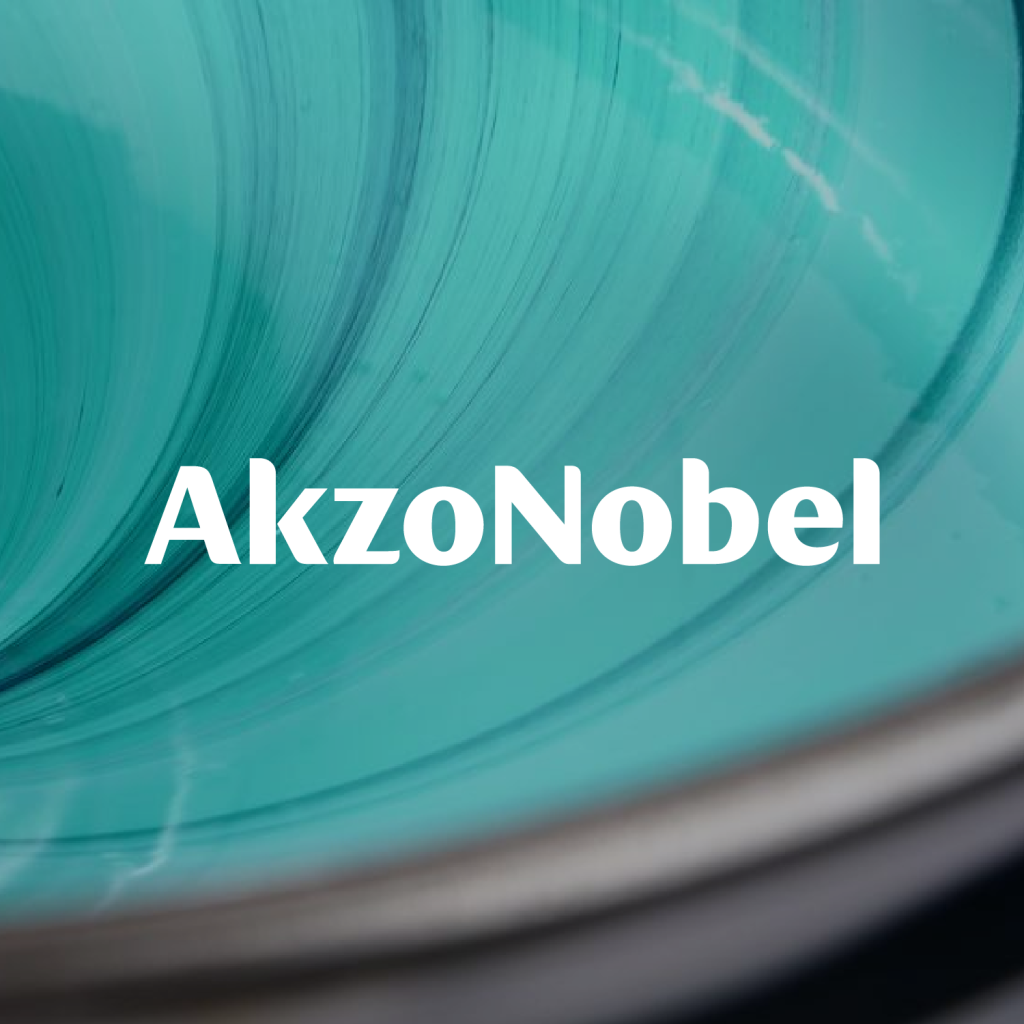
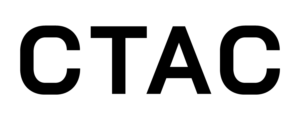
This is a CTAC partner story. Explore the inriver partnership with CTAC >.
AkzoNobel is a global paint and coatings brand that has been ‘bringing surfaces to life’ for over 200 years. Today, AkzoNobel is known for delivering high-quality paint solutions for a range of diverse sectors, from the aerospace and automotive industries through to household decoration, bringing color and imagination into homes across the globe. Headquartered in Amsterdam, here are key facts about AkzoNobel
- Active in 150+ countries worldwide
- An international workforce of 32,000+
- 8k-120k SKUs per business unit
In an increasingly competitive market, AkzoNobel aims to become a global industry leader that champions sustainable paints and coatings. To achieve this, the company identified a need to overhaul its global data governance strategy. With diverse business units located across the globe, the need for centralized management and maintenance of both technical and customer-facing data was key to ensuring AkzoNobel’s processes could support its growth ambitions within an uncertain world.
Ramon Delgado is AkzoNobel’s Process Manager Technical Data. Based in the Netherlands, Ramon has been with the company for over seven years and currently oversees AkzoNobel’s data governance transformation – a significant challenge for an established multinational brand. Here, Ramon reflects on how AkzoNobel has collaborated with inriver and Ctac to power this transformation.
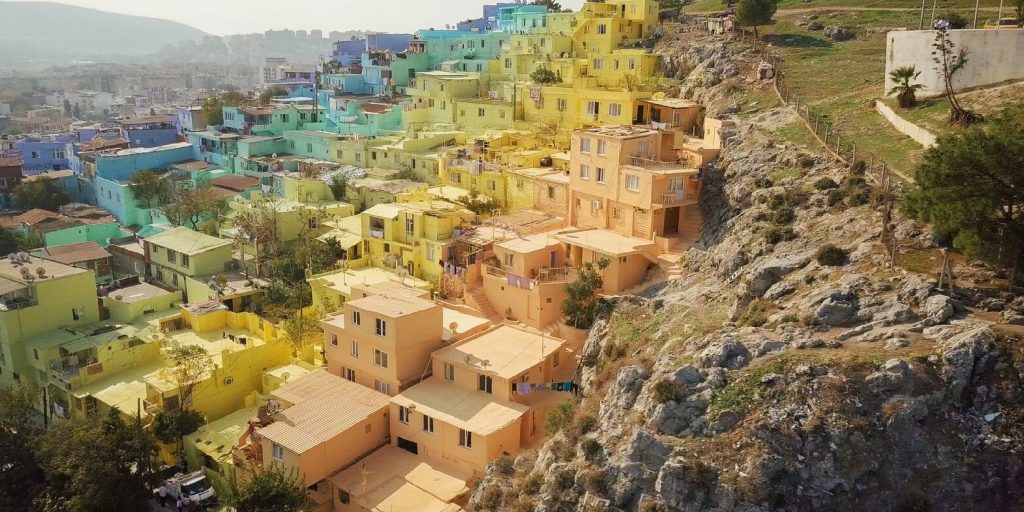
the challenge
As a result of its development and the scale of its operations, AkzoNobel had “no centralized governance in place regarding either the internal technical data or the output for technical customer-facing data,” notes Ramon. This absence of informational governance understandably caused issues – most acutely when it came to providing customers with the accurate technical data they required.
In part, this was caused by the company’s business units (BUs) largely working in silos when it came to data governance, employing localized domains and systems that were often maintained manually. “Some units had mature approaches to data collection and usage,” Ramon explains. “Others were still working with Excel documents and written notes.”
The challenge for AkzoNobel, therefore, was substantial yet clear. The creation of a closed system of data flow that delivered a single source of accurate, reliable information throughout all internal and external-facing operations.
However, the right solution for AkzoNobel would need to overcome two sizeable hurdles.
Firstly, with so many existing data management practices, it was imperative to find a solution that could communicate and integrate with these many different domains and systems in use to ensure a seamless navigation to that single source of truth.
Secondly, with operations spread across several diverse and distinct markets, any solution would have to provide localization capabilities to meet the requirements of the various BUs. Ensuring this would also aid internal buy-in of the migration of a new data model.
the solution
With their aims in place, AkzoNobel set about finding the right solution for their ambitions. As Ramon explains, internal stakeholder discussions included business engagement managers and enterprise architects.
“As a global company, we knew that having a comprehensive yet flexible PIM in place was essential to ensure communication between all our various source systems,” says Ramon. “inriver’s PIM solution was identified as the best way for us to do this.”
However, technology alone is only one part of the transformation AkzoNobel sought. Another crucial aspect was identifying an implementation partner who could be there at every step of the journey. In Ctac, AkzoNobel found that partner. As inriver’s largest partner in the Netherlands, Ctac has extensive experience in building out exactly the type of global solution AkzoNobel needed, and the relationship has been fruitful.
“We are in constant communication with Ctac,” says Ramon. “They are our first point of contact; the ones who help us define our capabilities. If we have requirements, we discuss it with them and inriver to find out if they can develop it into our solution.”
the results
With a challenge as substantial as the one facing AkzoNobel, Ramon was not expecting results overnight.
“I’ve been part of this project for almost two years, but we have been working with inriver for nearly five,” he explains. ‘The first BU was rolled out within 3 months and further optimized after it became operational. Following that, we started rolling out one BU at a time. This has made it a slow process, but if we want to get the inriver solution integrated successfully into our ecosystem it’s important that we take our time.”
“We started with around 25 ERP systems in place, and we are aiming for four or five in the near future. But it’s more than that. There are numerous programs and systems underneath those ERPs, and with the inriver solution we want to reduce those, too. It’s a big task.”
But despite the transformation still very much being a work-in-progress, there have already been some timely wins along the way.
“It’s now easier for us to create technical datasheets,” says Ramon. “And even though we still have some issues with our specific requirements when it comes to technical data, we are working with Ctac and inriver to find a new solution for our needs. That is the flexibility of PIM.”
“The biggest win, though, is that our people now know we are moving towards a reliable point for all our technical data, both for internal systems and customer-facing marketplaces. That’s the biggest change. We are now on a journey towards having a single source of truth.”
want to see the inriver PIM in action?
Schedule a personalized, guided demo with an inriver expert today to see how the inriver PIM can get more value from your product information.